I'm continuing my clay body reviews series with two very heavily grogged "sculpture" clays I've used.
Note that I currently practice in a community studio that glaze fires to cone 6 in oxidation, so my observations reflect that.
Standard 420 Sculpture:
- Cone 6: average shrinkage 8.0%, absorption 1.5%
- Light straw when fired to cone 6: more yellow/beige than most white stonewares so the color is something to consider in your final vision (or engobe in something else)
- So much grog that it's best described as working with wet sand, non-derogatory
- I've made complicated open coil-based structures with this clay that have been formed across many studio sessions over a couple days, and they've survived without cracking! Wet clay attaches readily to leather hard and even slightly dry clay. Wrapping my works in dry cleaning bags until done and dry before bisque was enough - I was worried I'd have to make a damp box, but not with this clay!
- The grog is white and grey, and it comes in a variety of sizes, including some that is visually rather large. The grog really shows if you sand to smooth the surface. I typically dislike how this looks - the result ends up looking more like concrete than clay.
- If you use this for functional ware or anything you move around a lot, you'll certainly want to sand the bottom since the groggy surface is extra rough to protect tables and counters. Burnishing alone doesn't usually make this clay smooth.
- Can be thrown when very soft, but your hands will feel scratched if you're not used to it!
- Angled slab joins join readily, and support coils press in quickly and easily.
- Some members of my studio prefer to make plates with this clay because the high level of grog significantly reduces warping. I personally prefer to make plates with clays with far less grog that I dry very slowly. High palpable grog content means a weaker object, and I prefer more strength in objects that are handled frequently.
- Can be marbled with 798, but needs to dry slowly.
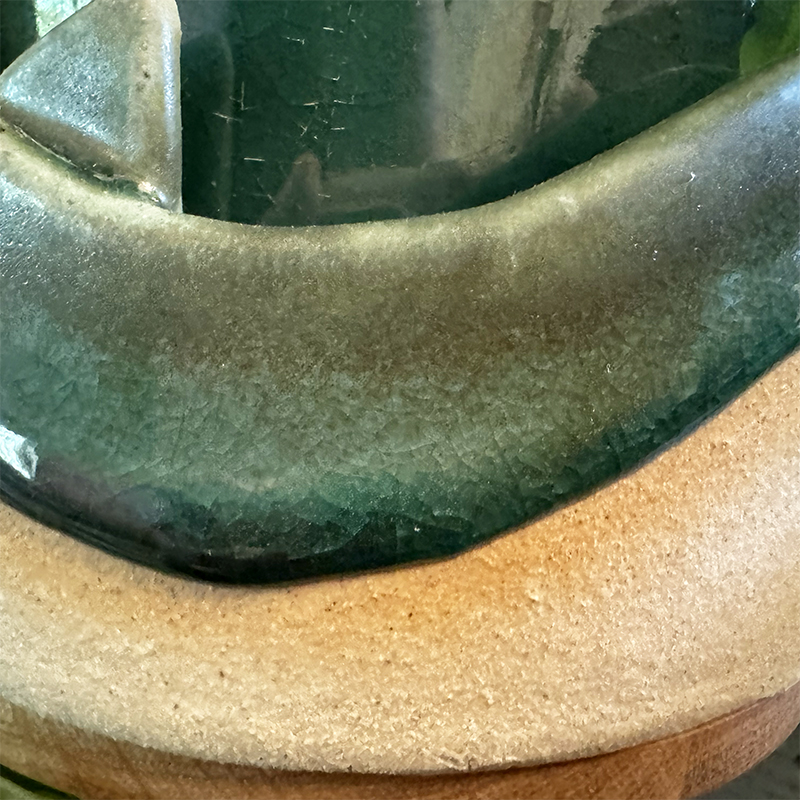
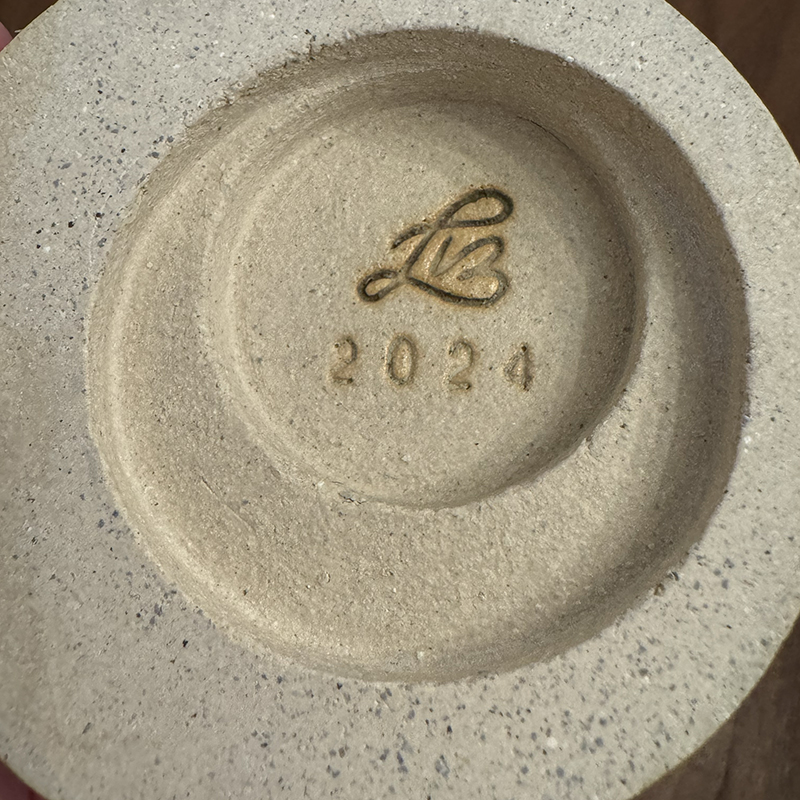
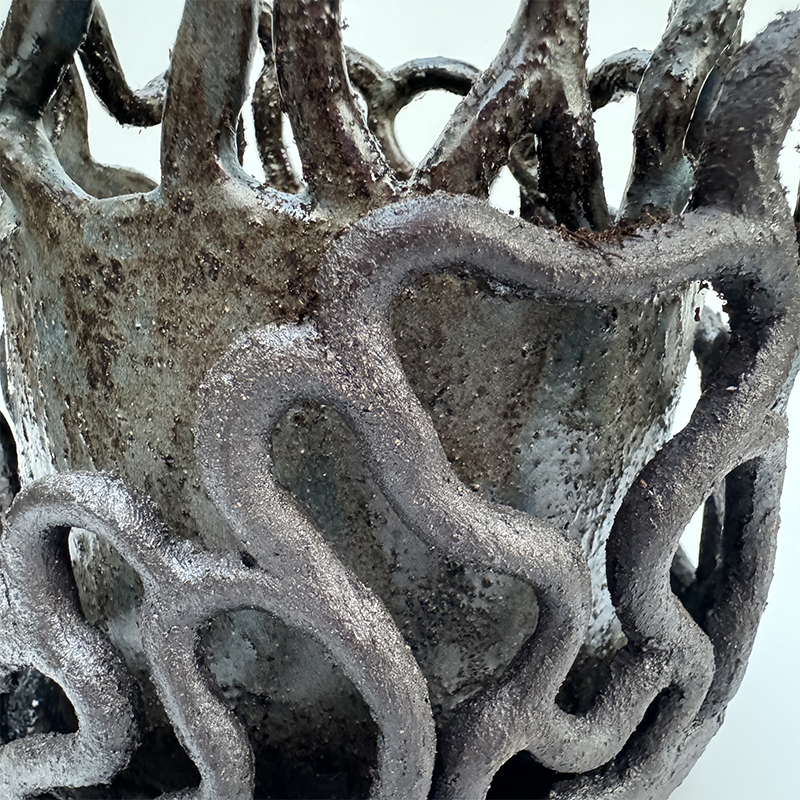
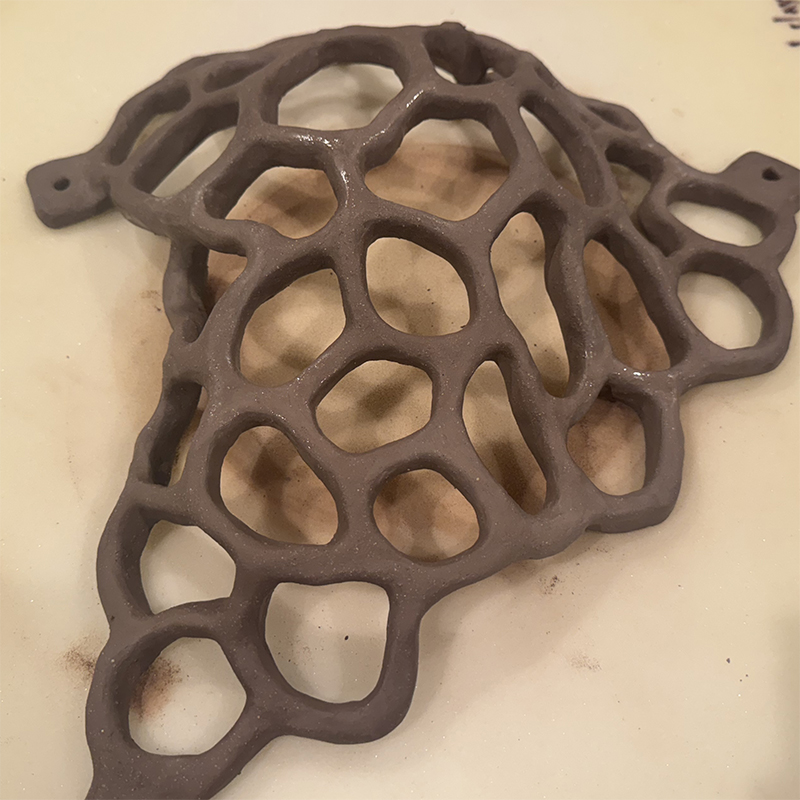
Standard 798 Black Sculpture:
- Cone 6: average shrinkage 10%, absorption 1.0%
- Dark brown when wet, fires to a gorgeous black at cone 6 when unglazed.
- Clear glazes will make this clay look brown, so you need to use a black like Coyote Black or Amaco Obsidian to preserve the black color if you want to glaze it.
- So much grog that it's best described as working with wet sand, non-derogatory.
- The grog is white, and provides a lovely contrast when on the surface or sanded to be revealed.
- Like 420, you'll probably want to sand the bottom of anything you'll pick up and put down more than once.
- Very similar working qualities to 420 - a true joy for handbuilding!
- Can be marbled with 420, but needs to dry slowly.